粉末冶金齒輪零件生產(chǎn)加工中的熱處理工藝
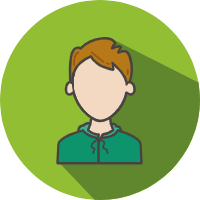
作者:翔宇粉末冶金制品
發(fā)布時(shí)間:2021-08-13 17:07:21
來(lái)源:本站 閱讀數量:1358次 點(diǎn)贊數量:1369次
粉末冶金齒輪是傳動(dòng)零件中的重要組成部分,是傳遞動(dòng)力的核心部件。所以粉末冶金齒輪必須具有高硬度、高強度、高密度等特點(diǎn)。如何用熱處理的方式提高粉末冶金齒輪的硬度和強度是粉末冶金齒輪生產(chǎn)加工中的必要環(huán)節。
粉末冶金齒輪和其他金屬材料一樣可以通過(guò)熱處理的方法改善其力學(xué)性能。應用在粉末冶金齒輪中的熱處理方法有退火、正火、淬火、回火、以及滲碳、滲氮和碳氮共滲等。這些方法無(wú)疑可以大大的提高粉末齒輪的力學(xué)性能,但是由于粉末冶金齒輪的獨特性,在選擇熱處理的方法和工藝條件時(shí),不能完全參照致密材料,必須要進(jìn)行合理的調整以適合粉末冶金齒輪的處理,否則會(huì )得不到熱處理的效果,甚至造成毀壞性的結果。采用熱處理改善粉末冶金齒輪性能的材料主要是鐵系合金(燒結鋼)。
粉末冶金齒輪燒結鋼在熱處理中要注意這幾點(diǎn)情況:
1.燒結鋼的空隙具有隔熱的作用,因此與致密鋼相比,燒結鋼導熱率低,熱量難于散失,導致淬透性差。
2.組織均勻性對奧氏體化的影響,燒結鋼組織均勻性因受到碳的分布不均勻等因素影響而變差。致使其奧氏體均勻化的溫度和時(shí)間要比致密鋼高得多,在相同的條件下,達到完全均勻化的時(shí)間要高出50%。如果燒結鋼中添加有合金元素則均勻化溫度更高,時(shí)間更長(cháng)。
3.空隙對碳含量的影響,由于燒結鋼中孔隙的存在,如采用與致密鋼相同的方法進(jìn)行處理,在處理過(guò)程中容易發(fā)生氧化和脫碳。所以對于含有6%孔隙的燒結鋼熱處理要在保護氣氛下或埋入固體填料(如分解氨、天然氣轉化氣體、木炭、鑄鐵屑等)中進(jìn)行。此外由于孔隙的存在以及密度不均勻,容易造成淬火裂紋和變形。
粉末冶金齒輪幾種常用的熱處理方法:
1.退火和正火,退火和正火是燒結鋼生產(chǎn)上應用的預備熱處理工藝。退火和正火的目的是消除內應力,調節材料的組織結構,從而調節鋼的力學(xué)性能和工藝性能,為下道工序做好組織和性能的準備,如在復壓、整形、切削等加工前要經(jīng)過(guò)退火處理。對于使用要求不高的機械零件,退火和正火產(chǎn)品也可作為成品使用。
2.淬火,將燒結鋼加熱到臨界點(diǎn)以上的溫度,保溫以后以大于臨界的冷卻速度,快冷到馬氏體組織的熱處理工藝稱(chēng)為淬火。淬火是燒結鋼用的最多的熱處理方法,通過(guò)淬火得到的馬氏體組織以提高燒結鋼的強度、硬度和耐磨性能。燒結鋼的淬火原理和工藝基本上與致密鋼相似。所不同的是燒結鋼淬火過(guò)程需要在中性或滲碳性氣氛中進(jìn)行,以防止孔隙表面氧化。由于燒結鋼的孔隙特征,通常是采用油淬,其淬火工藝包括加熱奧氏體化、淬火和回火。
3.回火,淬火之后必須回火?;鼗鹁褪菍⒋慊痄摷訜岬?80℃以上的溫度,保溫以后以適當方式冷卻到室溫的熱處理工藝?;鼗鸬哪康挠袃蓚€(gè),一個(gè)是消除內應力,降低材料的脆性?;鼗鹩址譃?,低溫回火、中溫回火和高溫回火。
粉末冶金齒輪的幾種表面硬化處理:
1.粉末冶金齒輪表面滲碳可以進(jìn)一步提高其表面的硬度。滲碳是用含碳的氣體、液體或固體作為滲碳劑,在高溫下使碳原子擴散至零件的表面與鐵反應,形成更多的滲碳體Fe3C。滲碳量越高,則形成滲碳體的量越多,滲碳層的深度和表面硬度也越高。滲碳所關(guān)心的問(wèn)題是滲碳層的深度和硬度。滲碳層的深度一般在0.5-2.5mm。粉末冶金齒輪零件滲碳主要存在的問(wèn)題是表面滲碳層的硬度。由于鐵基粉末零件存在孔隙的原因,碳原子有可能通過(guò)孔隙向零件的內部擴散,無(wú)法形成清晰的滲碳層,并且碳過(guò)多地向內部擴散會(huì )增加零件的脆性,無(wú)法發(fā)揮表面硬度高、內部強、韌性高的特性。所以孔隙高的零件不適合滲碳。
滲碳一般在高于740℃的溫度下進(jìn)行??紫抖刃∮?0%的鐵基零件,其最佳滲碳溫度為920-940℃。滲碳溫度越低,零件的撓曲變形就越小。所以在精度要求高的情況下,應采用860℃的低溫滲碳。滲碳處理后一般都要進(jìn)行淬火,以在表面得到更高硬度的馬氏體組織。滲碳淬火的淬火有兩種方式。一是直接淬火,即在冷卻到750-850℃直接進(jìn)行油淬,這種方法得到的組織較粗大,因為滲碳中奧氏體晶粒已粗化,力學(xué)性能降低;另一種方法是先將滲碳齒輪冷卻,然后采用燒結鋼的淬火工藝,進(jìn)行淬火。這種方法可克服直接淬火的確定,得到更優(yōu)異性能的粉末冶金齒輪。
2.齒輪表面滲氮,滲氮即含氮氣體與燒結鋼接觸,氮原子擴散至燒結鋼的表面,與鋼中的合金元素鉻、鋁、鉬、鎳、鎢反應并形成氮化物的過(guò)程。經(jīng)過(guò)滲氮使零件表面硬度進(jìn)一步得到提高。滲氮可單獨進(jìn)行,也可碳氮共滲。滲氮的方法是將齒輪升到495-565℃的溫度,通入氨氣,由氨氣中分解出的具有很高活性的氮原子對零件表面進(jìn)行淡化。對于粉末冶金齒輪滲氮最大的難點(diǎn)也是孔隙??紫哆^(guò)多無(wú)法形成滲氮層,在齒輪的內部生成氮化物會(huì )使零件變脆。
3.碳氮共滲,即在粉末冶金齒輪表面同時(shí)深入碳和氮,進(jìn)一步提高零件表面的硬度和耐磨性。碳氮共滲的方法是在滲碳過(guò)程中加入氨,這樣再深入碳時(shí)也滲入氮。碳氮共滲的溫度要低于單獨滲碳的溫度(低55℃左右),時(shí)間也較短些。碳氮共滲的零件密度應保持在6.85g/cm3,對于滲銅和高密度(7.2g/cm3)則非常有效。
4. 高頻淬火,粉末冶金齒輪高頻淬火是工件表面淬火的一種方法,即將工件置于線(xiàn)圈中,通入高頻電流,在高頻電流產(chǎn)生的交變磁場(chǎng)作用下,工件的表面將產(chǎn)生感應電動(dòng)勢及渦旋電流。由于集膚效應,感應渦流主要集中在工件表面,使表面產(chǎn)生高溫。高頻淬火即是利用這種加熱原理,將工件表面快速加熱到高溫,然后淬火,以獲得表面淬火 組織。需要耐磨的粉末冶金齒輪 相當一部分采用高頻淬火的熱處理方式。粉末冶金齒輪采用高頻淬火的熱處理方式時(shí)必須要注意齒輪的自身密度,密度要達到6.85g/cm3,這樣才會(huì )達到齒輪自身的強度,在局部加熱與未加熱之間產(chǎn)生應力,不至于零件開(kāi)裂。
感覺(jué)小編寫(xiě)得不錯,給小編點(diǎn)個(gè)贊吧!
點(diǎn)贊最近更新
-
粉末冶金的技術(shù)以及常見(jiàn)瑕疵
時(shí)間:07-10 閱讀:11次
-
粉末冶金射出成型和模壓的成本
時(shí)間:07-09 閱讀:21次
-
不銹鋼粉末冶金和精鑄的區別
時(shí)間:07-08 閱讀:29次
-
粉末冶金件的碳氮熱處理工藝
時(shí)間:07-07 閱讀:36次
-
粉末冶金如何增加強度的方法
時(shí)間:07-06 閱讀:42次
-
粉末冶金模具與壓鑄模件的區別
時(shí)間:07-05 閱讀:49次
-
粉末冶金材料的熱處理工藝試驗
時(shí)間:07-04 閱讀:58次
-
氫氣在粉末冶金應用中的應用
時(shí)間:07-03 閱讀:54次
欄目
熱門(mén)閱讀
-
粉末冶金精度高嗎?精度可以達到多少?
時(shí)間:07-04 閱讀:9841次
-
粉末冶金強度多少?強度不足原因是什么?
時(shí)間:09-23 閱讀:7326次
-
粉末冶金與翻砂鑄造的優(yōu)劣對比
時(shí)間:08-25 閱讀:6718次
-
粉末冶金與壓鑄的的優(yōu)劣對比
時(shí)間:08-25 閱讀:6291次
-
粉末冶金與切削加工的優(yōu)劣對比
時(shí)間:11-16 閱讀:6097次
-
粉末冶金究竟是什么?其特點(diǎn)以及工藝流程怎么樣?立馬為你分享
時(shí)間:02-24 閱讀:5447次
-
粉末冶金強度怎么?為什么還被廣泛應用?
時(shí)間:10-29 閱讀:5439次
-
粉末冶金工藝優(yōu)缺點(diǎn)分析,一文讀懂
時(shí)間:07-08 閱讀:5302次
-
干貨:粉末冶金制品的13種成型技術(shù)
時(shí)間:12-16 閱讀:4229次
-
粉末冶金與沖裁成型的優(yōu)劣對比
時(shí)間:11-16 閱讀:3491次